According to data from the RAIN RFID Alliance, there are approximately 25 billion RFID tags used for automated and non-contact identification worldwide each year, and this trend is increasing. Under such circumstances, one of the challenges facing RFID manufacturers includes the chip mounting process, which connects the semiconductor chip and the antenna together.
In order to meet this challenge, Italian RFID label and solution provider LAB ID has cooperated with German industrial adhesive company DELO.
LAB ID provides customized UHF RFID and NFC tags, as well as dual-frequency RFID tags that combine these two technologies. The company also provides services such as inlay design, software and hardware integration, and tag reading platforms. The company's UHF RFID tags are mainly used for logistics, supply chain management and warehouse management, while NFC tags are used for brand protection and the transmission of product information via smartphones. In addition, DELO provides customized adhesives and equipment for applications in high-tech industries such as automobiles, optoelectronics, and electronics.
DELO Southern Europe sales engineer Stefano Farina (Stefano Farina) said that the production of RFID tags needs to be optimized to the smallest detail in order to achieve high yields and meet growing demand. "The chip connection process, including connecting the chip and the antenna, is very demanding and there are many challenges. One problem is that due to the continued miniaturization trend, the chips are becoming smaller and smaller."
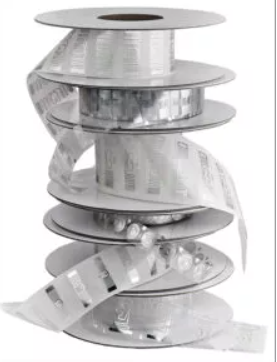
Each RFID tag consists of a chip and an antenna
Farina pointed out that process design is also very important. "From chip types, substrates and dispensing systems to adhesives and final product requirements, all parameters must be reproducibly matched to achieve an automated and efficient manufacturing process." To meet these challenges, LAB ID uses DELO's conductive epoxy Resin, and has used DELO's MONOPOX AC products for more than ten years.
These products are specially developed for chip connection applications to ensure maximum production efficiency. According to Farina, adhesives have a dual function. They ensure that the chip is immediately fixed to the antenna and provide electrical contact. The adhesive contains metal particles deposited between the bumps and the substrate. After the curing process, they exclusively conduct current in only one direction.
Before using adhesives in production, the company also conducted extensive functional tests to ensure the adhesive quality and durability of RFID tags. Even after simulated aging, the test showed good results in terms of reading range and bending strength. This includes storage at +85°C (+185°F) and 85% relative humidity, and temperature shock testing in the range of -40°C to +85°C. Farina said the adhesive has a mold shear strength of 50 MPa on standard substrates such as plastic and aluminum.
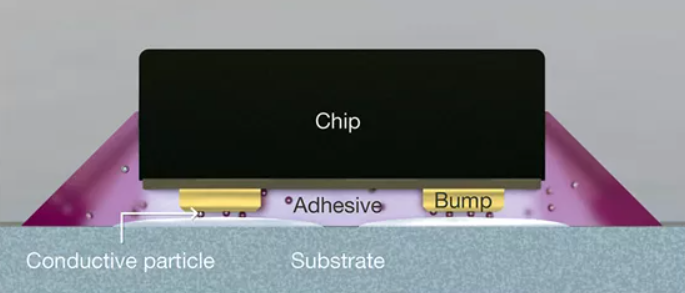
DELO conductive adhesive connects the substrate (antenna) and the chip and establishes a reliable electrical contact
In the next step, curing is carried out at 200°C (392°F) through a thermal electrode integrated in the process. Within one to two seconds, the adhesive is completely cured and electrical contact with the antenna is ensured. Then the completed RFID inlay can be further processed or coded accordingly.
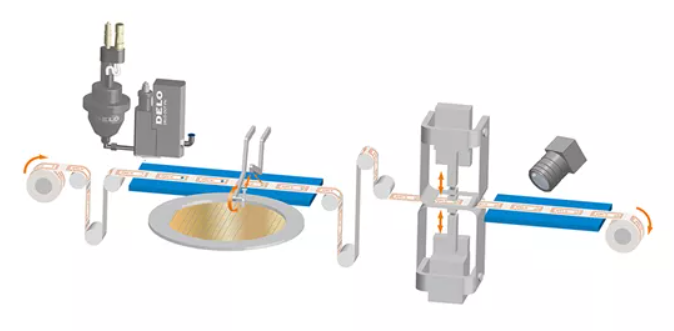
Due to the high requirements for micron-level precision, the production of RFID tags is a complicated process. It is not only necessary to ensure that the chip and antenna are fixed in place with a special adhesive, but also to provide electrical contact and meet high functional requirements. This complexity requires that the designed process can meet mass production and still maintain a high degree of reliability. Close cooperation between RFID suppliers and adhesive manufacturers is essential to implement efficient manufacturing processes and use high-performance RFID technology to support end users.