Rethinking the application of RFID in the warehouse
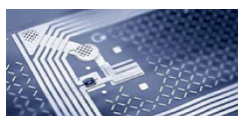
RFID technology has been around for a long time. It was originally used for inventory tracking purposes in warehousing and logistics in the early 21st century, but it has never really replaced the old bar code. The reason is not so much related to the maturity of the technology, as it is related to the cost of passive RFID tags.
In the United States at the beginning of the 21st century, the price of each label was between 15 and 25 cents. Although the price does not seem to be much, it cannot compete with ordinary barcode labels that are 0.2 cents and sometimes even free.
Around 2003, at the beginning of the modern RFID era, there was a talk that once the "five-cent label" was implemented, it would lead to a surge in RFID applications. But as far as the price point is concerned, we have not done this yet, and the reality is that the cost may need to be reduced to 1-2 cents to truly open the general-purpose inventory tracking application.
If the number of each label is multiplied by a single SKU in a typical distribution warehouse, the label can easily reach the order of millions. Since then, tag prices have been slowly falling, and the average price of passive RFID tags is now about 10 cents.
Nevertheless, the only point where the application of RFID technology really explodes lies in batch applications (multiple items stacked on a pallet are marked under a label) or high-value single products. Companies using this type of RFID technology are still struggling to keep the unit price at a relatively low level. In this case, data collection is either fully automatic (using RFID fixed access doors) or semi-automatic (using mobile devices to scan inventory).
When companies see the value of complete automation, that is, when data collection algorithms completely eliminate the presence of humans, they will adopt another method. For example, it is mainly used on conveyor belts, and RFID gates are installed to perform fast, reliable and fully automatic data collection without any manual intervention. The last thing to mention is that tracking devices usually use active tags for items.
Inventory bulk movement in automated warehouses
There are many completed projects on the market, including one that tracks inventory through pallets with RFID tags. For example, in the project of large flower growers, plastic raw material trays with RFID tags are used to track raw material receiving, inventory transfer, warehouse movement, and automatic distribution of materials to operations.
The deployment of RFID can not only automate product movement, but also can quickly scan inventory in a short period of time by using mobile RFID devices, thereby speeding up the quarterly inventory of inventory. In this way, the final products (such as flower pots) are loaded on a steel frame trolley, which is equipped with RFID hard tags, which can be automatically scanned when loading and unloading on the truck, and then shipped to department stores and retail stores across the country. The purpose of this is to track which retail outlets have received more floats than those returned due to improper handling.
Use RFID to track high-value items
In another type of RFID project, RFID tags are used to mark high-value commodities for inventory tracking purposes. For example, companies that distribute high-priced computer equipment for the telecommunications industry will use RFID tags to mark high-value items to speed up cycle counts.
But what’s interesting is that once the inventory is ready for shipment, barcodes are used instead of RFID tags to record conversions, because for shippers, high-value items are only a small part of the inventory they ship every day, so they are not equipped. RFID scanner.
In another case, retailers selling high-priced men's clothing will use RFID tags in their stores to simplify checkout scanning, weekly inventory counting, and automatic replenishment processes. This is a landmark project for high-end retailers. It not only simplifies inventory management and point-of-sale scanning, but also shows high-end customers the technological level and innovation of their stores.
RFID-based Kanban inventory management
In the past 15 years of RFID projects, there are also cases of RFID similar to Kanban inventory management. For example, the Kanban system is given an RFID tag attached to a plastic container used to store oil products. This project considered both active and passive tags, but in the end the customer chose the indestructible barcode tag instead of RFID, because automation was not very high on the priority list.
In another example, such as a customer of a meat processing plant. Each batch of meat is transported in a plastic box-shaped container with an active RFID tag affixed to it, which acts as a kanban. Since the kanban will be transported through various conveyor belts, the work order will be recorded through the RFID gate that passes through. Manually record the final production situation at the last station of the kanban container for inspection and packaging. After disinfection, the kanban container will return to the beginning of the production cycle and be associated with the next batch number.
Tracking equipment with active RFID tags
Active tags are not only more expensive than passive tags, but they also contain batteries to "broadcast" tag information to the environment. Therefore, active tags often appear in application scenarios such as device tracking. A heavy construction equipment leasing company is trying to complete an RFID project, using active RFID tags for equipment registration, leasing and inspection. Unfortunately, the project did not pass the pilot phase because the client merged with another company using a different ERP system.
All in all, RFID has very practical functions, but it still has a long way to go to reach the mainstream status in manufacturing and distribution.
In the United States at the beginning of the 21st century, the price of each label was between 15 and 25 cents. Although the price does not seem to be much, it cannot compete with ordinary barcode labels that are 0.2 cents and sometimes even free.
Around 2003, at the beginning of the modern RFID era, there was a talk that once the "five-cent label" was implemented, it would lead to a surge in RFID applications. But as far as the price point is concerned, we have not done this yet, and the reality is that the cost may need to be reduced to 1-2 cents to truly open the general-purpose inventory tracking application.
If the number of each label is multiplied by a single SKU in a typical distribution warehouse, the label can easily reach the order of millions. Since then, tag prices have been slowly falling, and the average price of passive RFID tags is now about 10 cents.
Nevertheless, the only point where the application of RFID technology really explodes lies in batch applications (multiple items stacked on a pallet are marked under a label) or high-value single products. Companies using this type of RFID technology are still struggling to keep the unit price at a relatively low level. In this case, data collection is either fully automatic (using RFID fixed access doors) or semi-automatic (using mobile devices to scan inventory).
When companies see the value of complete automation, that is, when data collection algorithms completely eliminate the presence of humans, they will adopt another method. For example, it is mainly used on conveyor belts, and RFID gates are installed to perform fast, reliable and fully automatic data collection without any manual intervention. The last thing to mention is that tracking devices usually use active tags for items.
Inventory bulk movement in automated warehouses
There are many completed projects on the market, including one that tracks inventory through pallets with RFID tags. For example, in the project of large flower growers, plastic raw material trays with RFID tags are used to track raw material receiving, inventory transfer, warehouse movement, and automatic distribution of materials to operations.
The deployment of RFID can not only automate product movement, but also can quickly scan inventory in a short period of time by using mobile RFID devices, thereby speeding up the quarterly inventory of inventory. In this way, the final products (such as flower pots) are loaded on a steel frame trolley, which is equipped with RFID hard tags, which can be automatically scanned when loading and unloading on the truck, and then shipped to department stores and retail stores across the country. The purpose of this is to track which retail outlets have received more floats than those returned due to improper handling.
Use RFID to track high-value items
In another type of RFID project, RFID tags are used to mark high-value commodities for inventory tracking purposes. For example, companies that distribute high-priced computer equipment for the telecommunications industry will use RFID tags to mark high-value items to speed up cycle counts.
But what’s interesting is that once the inventory is ready for shipment, barcodes are used instead of RFID tags to record conversions, because for shippers, high-value items are only a small part of the inventory they ship every day, so they are not equipped. RFID scanner.
In another case, retailers selling high-priced men's clothing will use RFID tags in their stores to simplify checkout scanning, weekly inventory counting, and automatic replenishment processes. This is a landmark project for high-end retailers. It not only simplifies inventory management and point-of-sale scanning, but also shows high-end customers the technological level and innovation of their stores.
RFID-based Kanban inventory management
In the past 15 years of RFID projects, there are also cases of RFID similar to Kanban inventory management. For example, the Kanban system is given an RFID tag attached to a plastic container used to store oil products. This project considered both active and passive tags, but in the end the customer chose the indestructible barcode tag instead of RFID, because automation was not very high on the priority list.
In another example, such as a customer of a meat processing plant. Each batch of meat is transported in a plastic box-shaped container with an active RFID tag affixed to it, which acts as a kanban. Since the kanban will be transported through various conveyor belts, the work order will be recorded through the RFID gate that passes through. Manually record the final production situation at the last station of the kanban container for inspection and packaging. After disinfection, the kanban container will return to the beginning of the production cycle and be associated with the next batch number.
Tracking equipment with active RFID tags
Active tags are not only more expensive than passive tags, but they also contain batteries to "broadcast" tag information to the environment. Therefore, active tags often appear in application scenarios such as device tracking. A heavy construction equipment leasing company is trying to complete an RFID project, using active RFID tags for equipment registration, leasing and inspection. Unfortunately, the project did not pass the pilot phase because the client merged with another company using a different ERP system.
All in all, RFID has very practical functions, but it still has a long way to go to reach the mainstream status in manufacturing and distribution.