How retailers use RFID to prevent theft
In today's economic situation, retailers are facing difficulties. Compared with e-commerce companies, highly competitive product pricing, unreliable supply chains and rising management costs put retailers under tremendous pressure.
In addition, retailers need to reduce the risk of store theft and employee fraud at every step of their operations. In order to effectively deal with such challenges, many retailers are using RFID to prevent theft and reduce management errors.
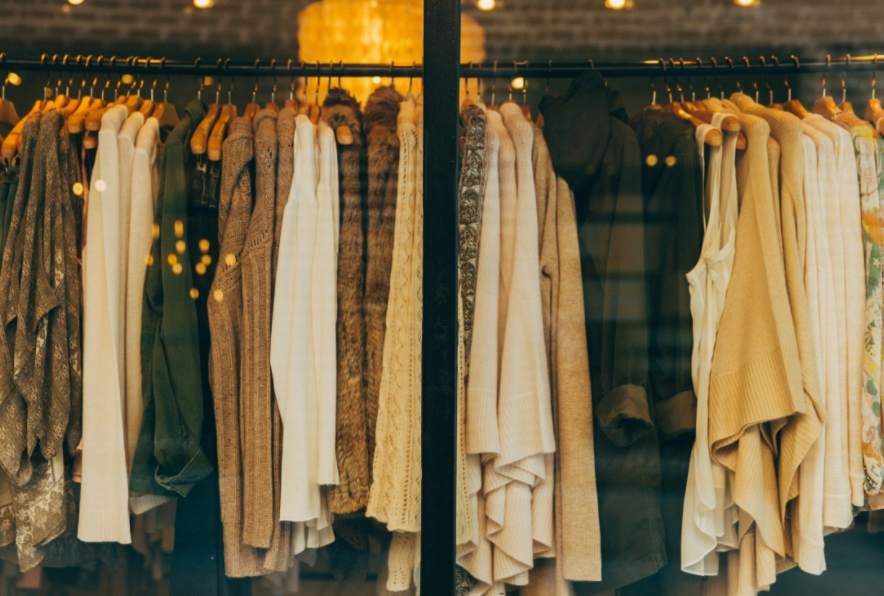
According to the National Retail Fund (NRF), US retailers lose more than $60 billion in revenue each year due to theft and employee fraud. NRF also found that retailers suffer inventory shrinkage of up to 1.6% each year (a term used to express inventory loss). For a company like Wal-Mart, this means that it will lose about $8 billion in revenue within a year. Using RFID to prevent theft and fraud and combat counterfeit products is the best way for retailers to cope with the rising rate of theft.
Why use RFID to prevent theft and reduce retail costs
Now the retail industry is becoming more and more complex in terms of processes and technology adoption. Retail companies now need sophisticated technology to ensure the bottom line of issues such as asset protection, loss prevention, and information security. It is estimated that two-thirds of the retail industry’s annual losses are caused by inventory losses and employee theft.
Retailers are also using RFID technology to follow the modern trend and improve the management of every step in their inventory management and consumer fulfillment business. The commodity-level RFID system improves inventory accuracy and process tracking, while allowing retailers to effectively investigate and manage problems.
The following are four ways that RFID helps retailers manage and prevent losses throughout the industry:
Retailers are also using RFID technology to follow the modern trend and improve the management of every step in their inventory management and consumer fulfillment business. The commodity-level RFID system improves inventory accuracy and process tracking, while allowing retailers to effectively investigate and manage problems.
The following are four ways that RFID helps retailers manage and prevent losses throughout the industry:
Fully supervise all company assets using RFID
At first, the company only used RFID technology to track expensive assets. When distributing tablets or laptops to employees, the company can add a label to prevent someone from leaving the office building with the device without authorization. As the cost of this technology decreased and became easier to implement, retailers quickly began to adopt RFID systems to manage inventory throughout the supply chain.
Most people find that although inventory management and inventory replenishment are the main goals of deploying RFID, its return on investment (ROI) far exceeds expectations. In the retail industry, the reduced cost of RFID implementation makes it an ideal choice for establishing a complete asset management and supervision system. For retailers, if someone tries to sneak out of the gate with stolen goods, the use of RFID readers at all exit locations can trigger an alarm. Electronic commodity surveillance (EAS) systems are also now commonplace, which provides additional benefits for retailers.
Readers at all exits identify the RFID tags on individual items, which can provide decision makers with valuable data, such as which items are easy to be stolen, and remind employees of any attempted theft; it can also indicate the ideal trend of the product and implement it. Additional security management to curb losses caused by theft; it can also quickly replace stolen products to avoid sales losses caused by out of stock.
Most people find that although inventory management and inventory replenishment are the main goals of deploying RFID, its return on investment (ROI) far exceeds expectations. In the retail industry, the reduced cost of RFID implementation makes it an ideal choice for establishing a complete asset management and supervision system. For retailers, if someone tries to sneak out of the gate with stolen goods, the use of RFID readers at all exit locations can trigger an alarm. Electronic commodity surveillance (EAS) systems are also now commonplace, which provides additional benefits for retailers.
Readers at all exits identify the RFID tags on individual items, which can provide decision makers with valuable data, such as which items are easy to be stolen, and remind employees of any attempted theft; it can also indicate the ideal trend of the product and implement it. Additional security management to curb losses caused by theft; it can also quickly replace stolen products to avoid sales losses caused by out of stock.
商品级RFID标签提供库存可见性
在跟踪整个零售供应链中的所有产品时,RFID发挥了奇妙的作用。企业可以部署该技术来管理和跟踪库存中的每件物品,从源头到最终目的地。通过与制造商合作,零售商还可以使用RFID传感器来记录特定商品的价格、质量信息、运输细节和预定目的地。RFID标签可以根据所收集的数据,为企业在供应链的每个阶段提供明智的业务决策、需求分析和防止库存收缩。
在库存跟踪过程中,企业可以知道货物当前所在的位置、物品数量以及在运输途中丢失的物品需要多长时间来更换。这一切都得益于RFID监控了所有的信息。还有一个好处是,一旦员工知道每件物品都处于被跟踪状态,员工盗窃意图就会相对减弱。使用RFID来防止零售盗窃可以提高员工的责任感,同时帮助优化上游分销流程。
Use RFID to accurately track the data review process
Compared with other technologies such as barcodes, RFID chip technology can store specific information at different stages of the label. Companies can add timeline nodes for products arriving at specific locations, track the time between destinations, and record who has accessed the product or inventory at each step of the entire supply chain. Once the product is lost, the company can find the personnel who visited the batch, review the upstream process and accurately identify where the item was lost.
RFID sensors can also measure other factors in transportation, such as recording item impact damage and transportation time, as well as the exact location in the warehouse or store. Such inventory monitoring and audit trails can help reduce retail losses in weeks instead of years, thereby providing an immediate return on investment. The management can call up the complete historical record of any item in the entire supply chain, and provide assistance when the company investigates missing items.
RFID sensors can also measure other factors in transportation, such as recording item impact damage and transportation time, as well as the exact location in the warehouse or store. Such inventory monitoring and audit trails can help reduce retail losses in weeks instead of years, thereby providing an immediate return on investment. The management can call up the complete historical record of any item in the entire supply chain, and provide assistance when the company investigates missing items.
Use RFID to track employees and products to prevent theft
Another way for retailers to reduce losses and determine who is responsible for the losses is to track the movement of all employees. If employees use access cards to pass through different areas of the store, the company can determine where everyone was when the product was lost. RFID tracking of products and employees allows the company to find possible suspects only by extracting the visit history of each employee.
Combining this information with a security surveillance system, the company will be able to build a comprehensive case against thieves. The FBI and other organizations have used RFID tags to track visitors and people in their buildings. Retailers can use the same principle to deploy RFID in all their locations to prevent fraud and theft.
Combining this information with a security surveillance system, the company will be able to build a comprehensive case against thieves. The FBI and other organizations have used RFID tags to track visitors and people in their buildings. Retailers can use the same principle to deploy RFID in all their locations to prevent fraud and theft.